2021 FSA Posters
P023: ITERATIVE LEARNING CONTROL OF PEEP WITH AN ON/OFF EXHALATION VALVE IN AN EMERGENCY USE VENTILATOR
Gordon Gibby, MD; Anthony DeStephens; Steven Nystrom; William Johnson; Ilana Zarour; Samsun Lampotang; University of Florida
Introduction: For the COVID-19 pandemic, we designed, built and evaluated an inexpensive (<$300 cost of materials), single-use pneumatic circuit, PanVentTM ventilator, assembled in 2 – 4 person hours with hand tools from non-ventilator supply chain parts available within days in quantities of 100,000s. Anticipating that add-on, spring-loaded Positive End Expiratory Pressure (PEEP) valves will be scarce during a ventilator shortage and to reduce parts count, we designed the exhalation valve to function as a PEEP valve also. Additionally, wanted to eliminate the pressure oscillations that add-on PEEP valves induce during exhalation that generate noise and affect the accuracy of the volume measurement from flow sensors. We explored if we could exploit the repetitive, cyclical nature of each breath, specifically each exhalation, by using memory-based control algorithms, like iterative learning control (ILC), that learn from exhalation to exhalation to, over multiple breaths, reduce PEEP error and accurately control PEEP at the set level.
Methods: We sampled airway pressure (BMP280, Bosch) at the breathing circuit elbow with an absolute pressure sensor referenced to a separate measurement of ambient pressure (BMP280). The PanVentTM ventilated a test lung with adjustable compliance C and resistance R (Michigan Instruments TTL) according to the ISO 80601-2-80 test protocol for 30 breaths at each R, C combination. Our software in C/C++ ran on an Arduino Nano microcontroller. The exhalation valve is a $13, on/off, lawn sprinkler valve (Model MME-DQDS-D012, Orbit) pressurized shut by low-pressure gas (~5 psig) controlled by a 3-way, normally closed solenoid valve (Model 57460P#, Clippard). The ILC algorithm closes the exhalation valve only once within one exhalation to avoid inducing pressure oscillations from multiple valve closings. Attained PEEP pressure is measured in cm H2O 400 milliseconds after exhalation valve closure as expiratory flow and pressure wane. PEEP error is: set PEEP – attained PEEP. If PEEP error is negative, the exhalation valve was closed too late and allowed too much gas to flow out from the lung, not trapping enough residual gas volume in the lung to reach the set PEEP. On the next exhalation, the valve closes earlier using time steps that are dependent on the magnitude of PEEP error. Conversely, if PEEP error is positive, the ILC opens the valve later on the next exhalation. We used asymmetric time steps when shifting valve closure time (larger time steps when driving PEEP down vs. up) to prevent pressure oscillations. Iterative learning occurs over multiple breaths until the PEEP error is within the specified bounds (±1 cm H2O).
Results: ILC control reduced pressure oscillations and provided PEEP accuracy of ≤10%. Fig. 1 shows the pressure plot at C 0.01 L/cmH2O, R 50 cmH2O/L/s, tidal volume 300 mL, respiratory rate 20 bpm and PEEP 10 cm H2O. PEEP error was ≤10% and within bounds in 7-18 breaths with ILC (Table 1)
Conclusion: ILC control is accurate and reduces pressure oscillations when controlling PEEP via a $13, disposable, on-off valve when ventilating a test lung with an emergency use ventilator according to the ISO 80601-2-80 test protocol.
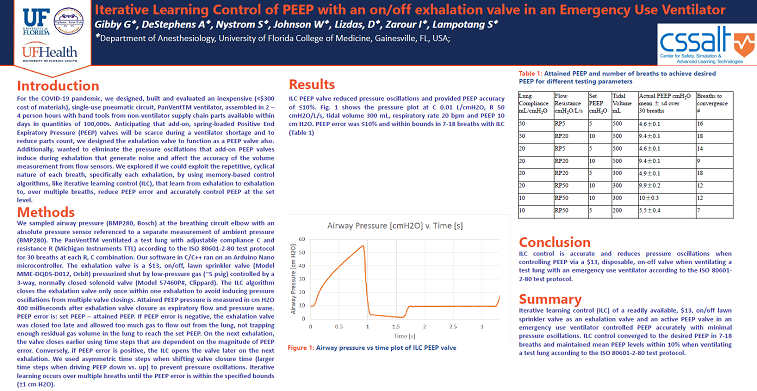